事例紹介
ホーム » 事例紹介
導入事例の紹介
01
稼働状況見える化による
業務効率化
従来人手で加工条件や稼働情報、検査結果を記録していたものを自動でデータベースへ記録し、グラフ化する
仕組みを導入しました。 その結果、生産状況の分析が容易になり品質向上や消耗品の故障予知などが可能となりました。
仕組みを導入しました。 その結果、生産状況の分析が容易になり品質向上や消耗品の故障予知などが可能となりました。
【事例】
生産情報取得
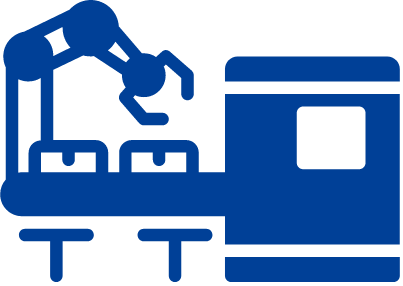
- 稼働状況
- 検査結果
- 装置条件
データベース格納
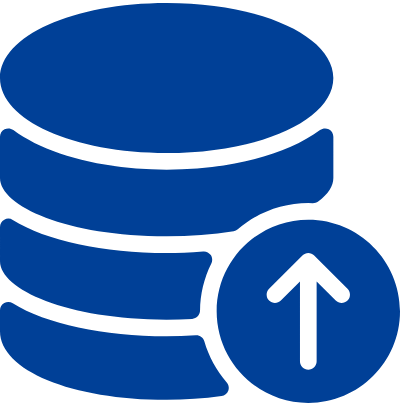
可視化・分析

- 品質向上(不良発生状況分析)
- 消耗品故障予知
02
装置条件の自動記録による
品質管理向上
従来人手で装置条件を管理していましたが、トラブル対応に追われて記録を忘れていたり、いつの間にか条件が変わっていたということが多々発生していました。
装置条件の自動記録を導入することにより、変更履歴を正確に管理でき、トラブル時の原因解明等の品質管理
向上に役立っています。
向上に役立っています。
【事例】
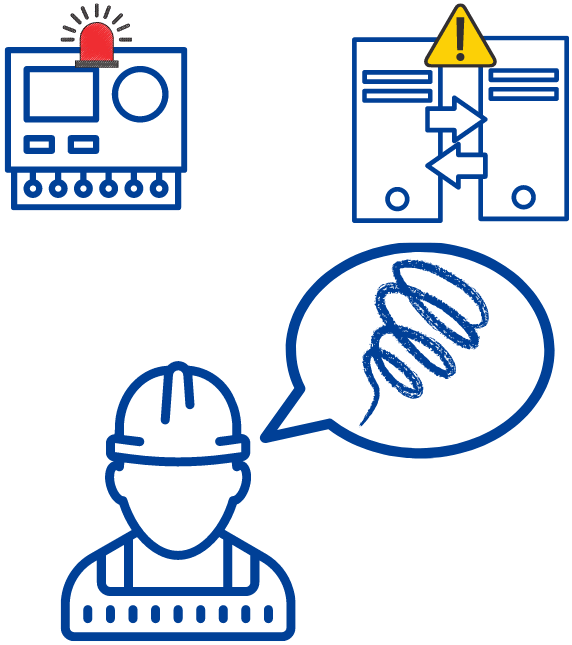
・深夜番でいつの間にか装置条件が
変わっていた、、、
・トラブル対応に夢中で変更前の装置条件を忘れてしまった、、、
・部品のロット間ばらつきで装置条件が変わってしまう→ロット毎の条件を確認したいけど記録がない、、、
- いつ・だれが・何の条件を・どう変えたか正確に記録
03
生産管理システム導入
による作業効率化
従来、生産計画作成・生産・帳票記入を個々に対応していたものを、データ連携することにより段取り時間の
削減や帳票記入時間の削減を実現しました。
削減や帳票記入時間の削減を実現しました。
【事例】
Before
Before
生産計画作成
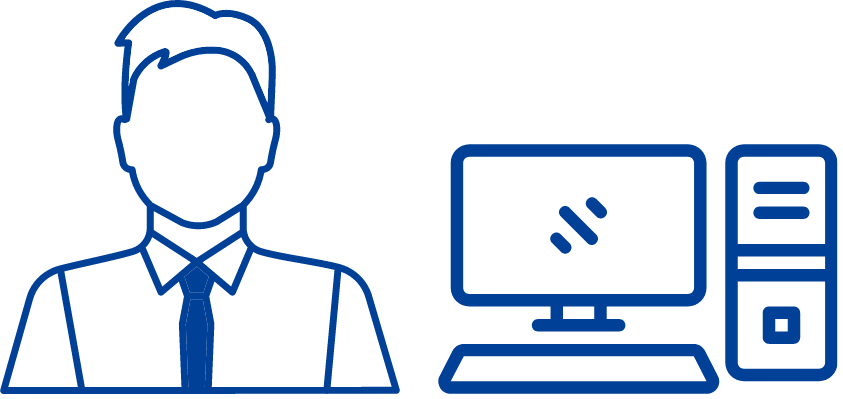
生産
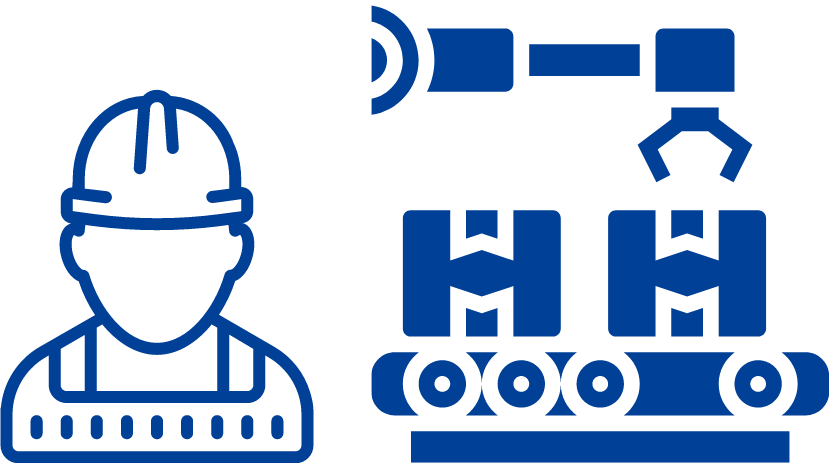
帳票記入
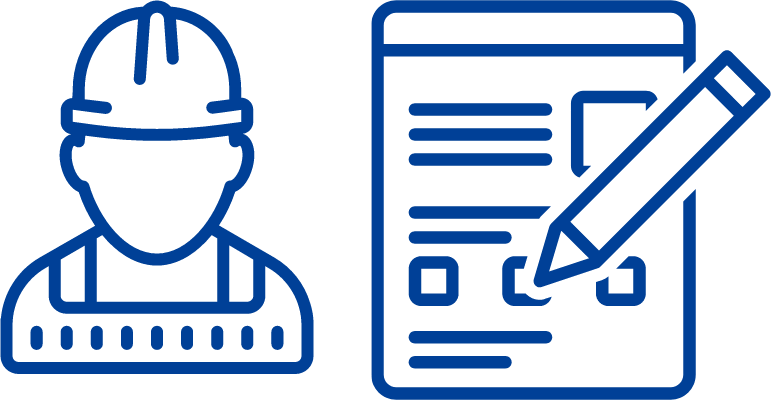
After
After
生産計画作成
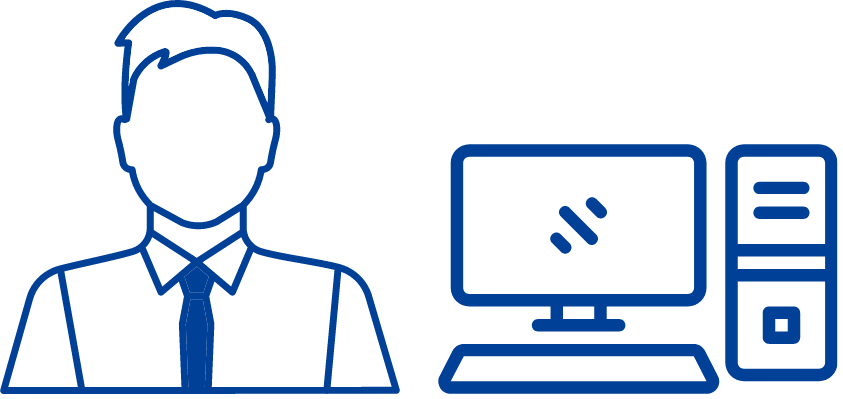
伝送
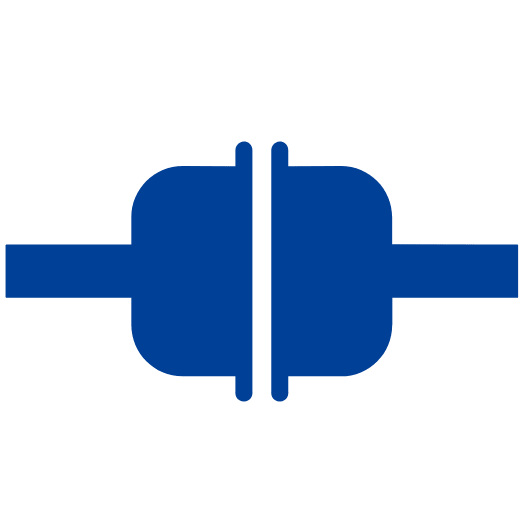
自動段取/生産
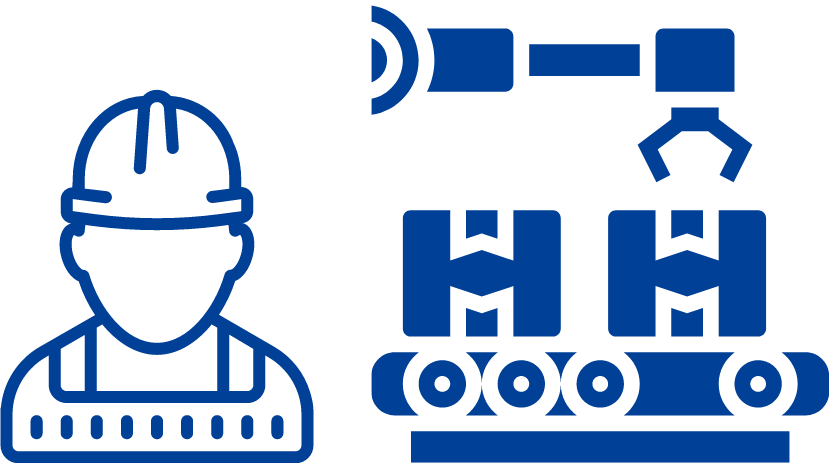
伝送
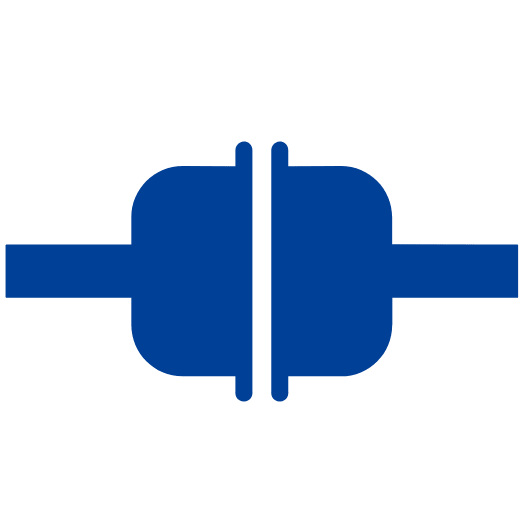
実績反映
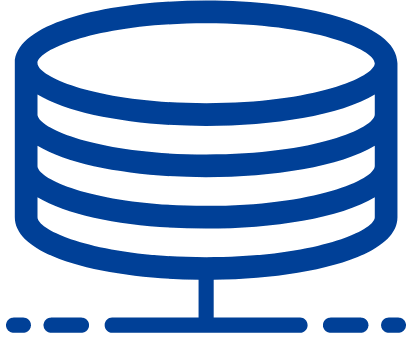
- 段取時間削減
- 帳票記入時間削減
04
IoT導入による在庫管理/
日報作成の効率化
従来、紙の記帳による在庫管理や日報作成を行なっていたものを、タブレット入力による管理へ変更しました。
これにより記入時間の削減とデータベース管理にしたことで日々の生産分析の簡易化を実現しました。
【事例】
製品管理票
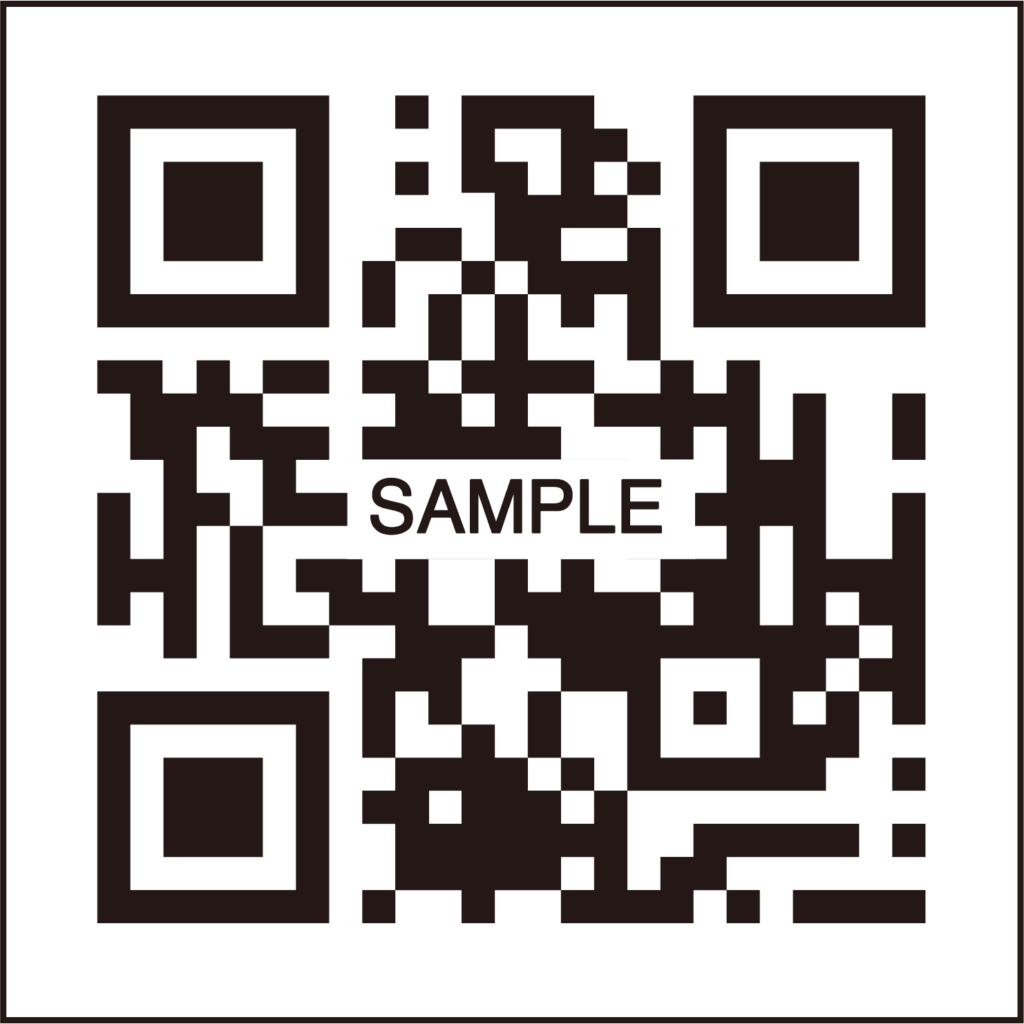
作業員がQRを読み取り
→実績入力
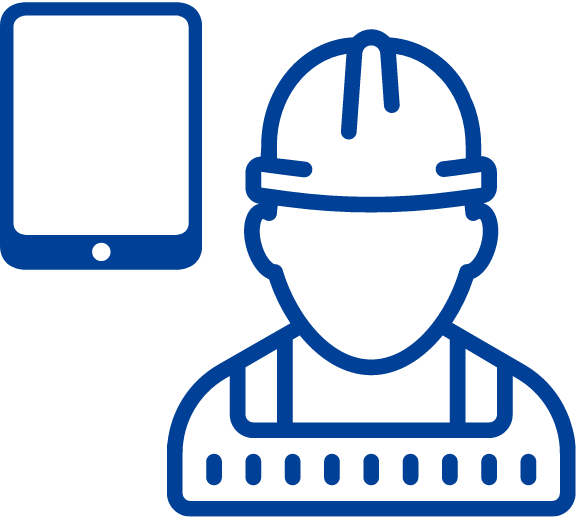
データベースに蓄積
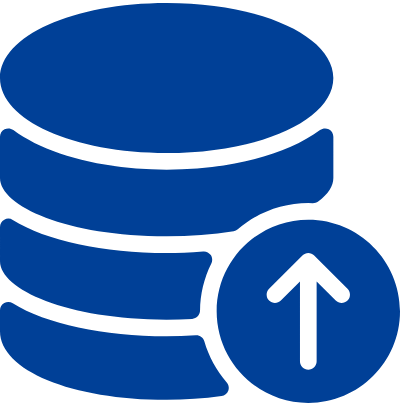
可視化
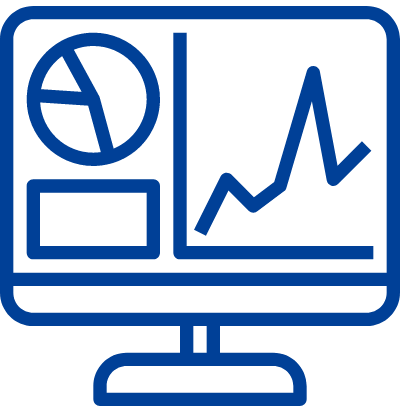
- 製品の加工状況をリアルタイムで把握、管理負荷低減
同様の手法で在庫管理も可能です
ご紹介した事例以外にも多数実績がございます。
まずはご相談ください。
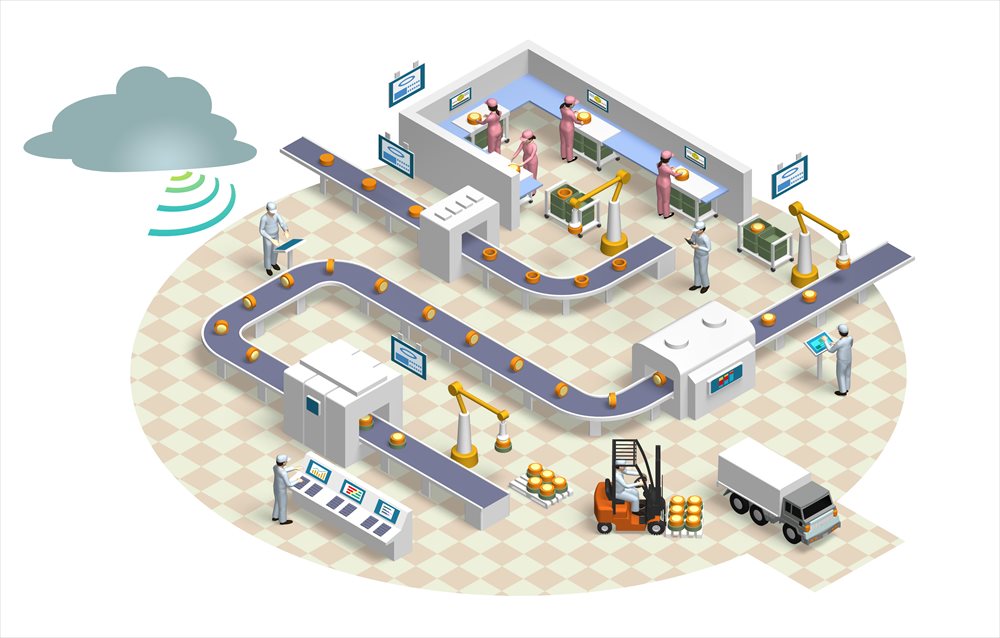
・生産/間接業務の課題抽出、効率化の提案
・各種課題に対する解決策立案
・システム導入支援(要件定義、仕様書作成、他)
・歩留まり向上、稼働向上支援
・その他お困りごと(オンライン会議導入、勤怠管理などなんでもご相談ください)