
設備停止が多く可動率が上がらない
設備の稼働状況の把握ができない
稼働状況を把握するシステムが欲しいが予算が足りない
こんなお悩みを抱えている中小企業の方は多いのではないでしょうか。
その悩みを解決できるツールの1つが稼働状況を見える化するアンドンです。
またすでにアンドンのような稼働状況見える化システムを導入している中小企業でも
上手く使いこなせない
メンテナンスが大変
こんなお悩みありませんでしょうか?
そこで今回は
アンドンってなに?
アンドンのメリット・デメリット
IoTで進化したデジタルアンドンとそのメリット
デジタルアンドンの導入方法
について解説します。
この記事を見ればIoTを活用した生産性アップと人材育成を同時に実現する手法を学ぶことができます。
ぜひ最後まで読んでみてください。
アンドンとは
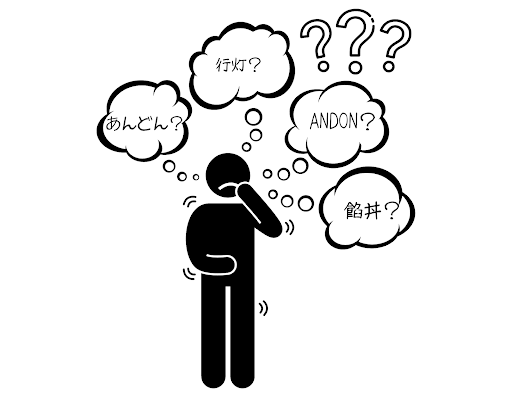
目次
アンドンとは製造ライン内の稼働状態を表示した電光掲示板のことです。
トヨタ生産方式の重要要素のひとつで「目で見る管理」をするためのツールです。
アンドンに表示する情報でライン内の作業者にアクションを促し効率良く生産ラインを稼働させる目的で使用されます。
表示される情報は、主に下記の3つです。
・設備の稼働状況(設備異常・消耗品交換・品質チェックなど)
・作業指示
・生産進度
代表的なアンドンの例を下記で説明します。
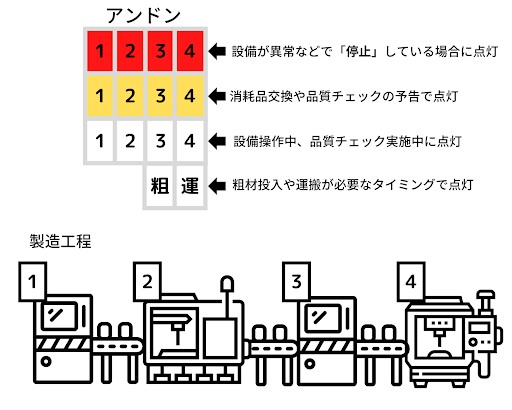
設備の稼働状況は各設備に割り当てられた工程番号と3色の表示灯で表現されます。
赤色の表示灯は設備が停止しているときに点灯します。
赤点灯時は可動率低下に直結する状態なので作業者に最優先で対応が求められます。
黄色の表示灯は刃具などの消耗品交換と品質チェックの事前予告として点灯します。この対応が遅れると設備が停止し赤色が点灯するのでその前に対応することが求められます。
白色の表示灯は設備操作中もしくは品質チェック作業中に点灯します。
(3色に加えて点灯と点滅で別の意味を持たせている現場も場合もあります)
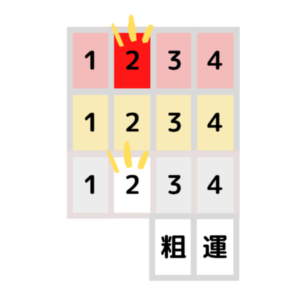
たとえば上の場合、
設備異常で工程2が停止していることが分かります。
同時に白色も点灯しているので、すでに作業者が設備異常の対応にあたっていることが分かります。
これによりほかの作業者は工程2に行く必要はなく別の仕事を優先する判断ができます。
このようにアンドンには3色のランプだけで必要な情報だけを伝える工夫がされております。
作業指示には専用の表示灯があり、粗材投入や運搬の発進が必要なタイミングを知らせます。

生産進度は計画数(その時点で生産すべき数)、実績生産数(その時点で実際に生産した数)を表示して把握することできます。
下記の例では5台分の生産遅れが発生していることがわかります。
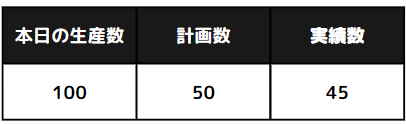
以上のようにアンドンは必要な情報を、必要なタイミングで必要な人に届けるためのツールです。
これはトヨタ生産方式のジャスト・イン・タイムに沿った考え方で効率的な生産には欠かせないものです。
従来型アンドンのデメリット
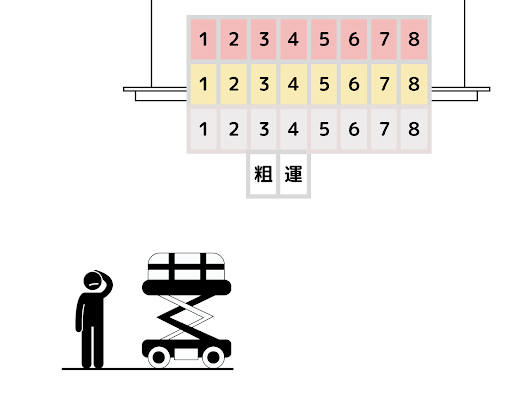
ただし従来型のアンドンには下記のデメリットもありました。
設置費が高い
メンテナンス時の安全面
ルールが理解しにくい
設置費が高い
アンドンはどこからでも見えるように高所に設置する必要があります。また設備数が多くなると大型になります。
そのため高所に大型の表示灯を設置することになり必然的に設置が高額になります。
メンテナンス時の安全面
従来型のアンドンは電球で点灯させているため、定期的に電球の交換が必要になります。
その交換作業が高所作業になることから安全面で課題があります。
ルールが理解しにくい
アンドンは3色のみで必要な情報を伝える工夫がされている一方で、そのルールに慣れるまでに時間がかかります。
とくに最近は外国人作業者が増えている現場も多く、理解が難しいため馴染みにくいものになっています。
デジタル化で進化したアンドン
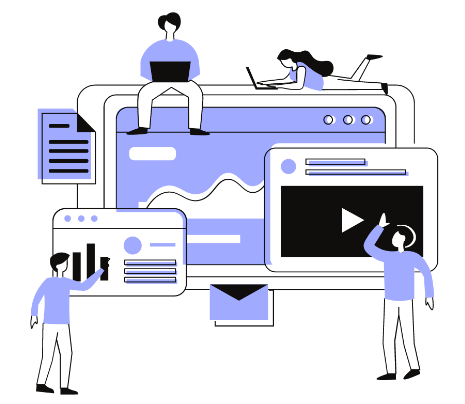
従来型のアンドンのデメリットを解消してくれるのがデジタルアンドンです。
設備と表示器をネットワークで接続し、デジタルで表示することができます。
デジタルアンドンのメリットは下記の3つです。
- 高所に設置する必要がない
- 直感的で分かりやすい
- どこからでも見える
- 作業員ごとに必要な情報だけを表示することができる
高所に設置する必要がない
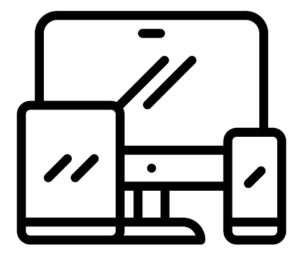
現在は表示器の選択肢が多くあります。液晶モニター、パソコン、タブレット、スマホ、スマートウォッチなどを使用することで設置する場所の制限がなくなります。
そのため高所に設置する必要がなくメンテナンスの費用面、安全面の課題も解消されます。
直感的で分かりやすい
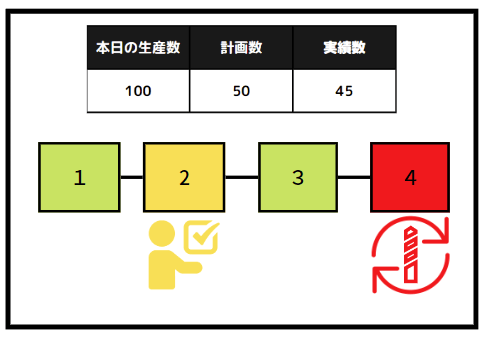
デジタル表示になると、設備配置やアイコン表示することもできます。
ラインの設備配置をそのまま画面上に描くことで直感的にどこで何が発生しているのかわかるようになります。
文字を使用する必要がないので外国人にとっても理解しやすいです。
上の絵の例では
工程1と3は「正常稼働中」
工程2は「もうすぐ品質チェックが必要」
工程4は「ドリル交換が必要で設備停止」
と各設備の状態が直感的に理解でき、従来型のアンドンよりも馴染みやすいです。
どこからでも見える
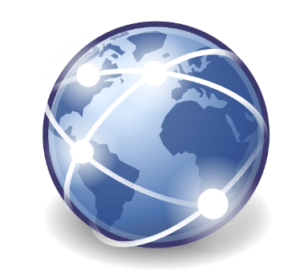
ネットワークに接続すれば場所を問わずどこからでも稼働状況を確認することができるようになります。
現場の作業者はもちろんですが、現場監督者が詰所で事務作業をしながらでも、経営者が外出中でも稼働状況を確認することができるようになります。
作業車別に必要な情報だけ表示することができる
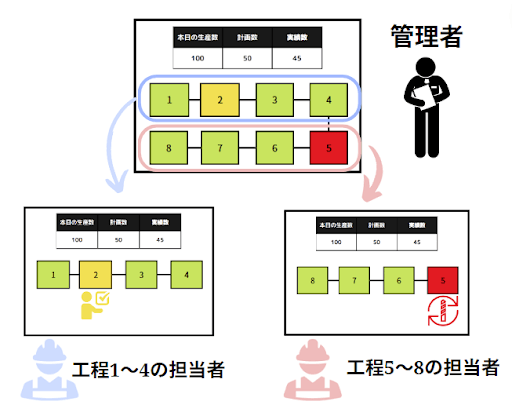
表示するデバイスが多様化したおかげで管理者や作業者ごとにそれぞれの必要な情報だけを表示することもできます。
上の例では管理者にはライン全体を、作業者には担当する設備だけを表示しています。
デジタルアンドン導入方法
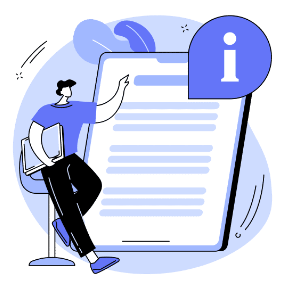
ここまでデジタルアンドンのメリットを紹介しましたが、
導入費用が高額になる
導入後のランニングコストが高額になる
IoT人材がいないからメンテナンスが不安
古い設備だからIoT導入はできない
このようなイメージがあり導入を諦めている中小企業も多くあると思います。
実はこれらの課題はやり方次第で解消できます!
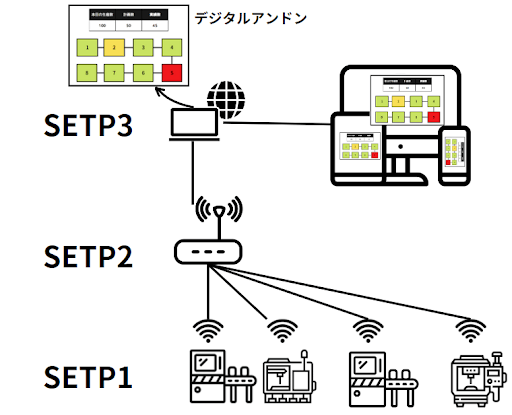
導入に必要なのは大きく3つのSTEPです。
STEP1:設備の信号を出力する
STEP2:設備からの信号を集約してネットワークに接続する
STEP3:アンドン(稼働状況)を表示する画面を作成する
SETP1:設備の信号を出力する
代表的な出力方法を下記の表にまとめました。
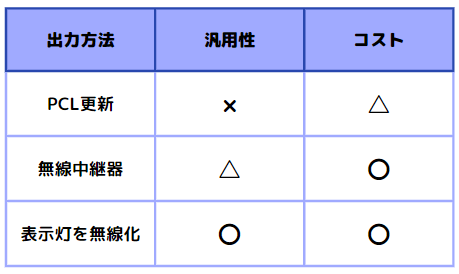
すでにPLCを使用している設備にはPLCを更新する方法があります。
PLCを使用していない設備でもアナログ信号をデジタル信号に変換して送信できる無線中継器を使用する方法があります。
制御盤内のリード線やIO線に無線中継器を接続するだけで出力することができます。
(例としてはアローセブン社の無線信号中継器を使用することで信号の出力が可能です。)
さらに制御盤が無い設備でも異常表示灯などの表示灯があればその表示灯を無線化して出力することができます。(例としてはパトライト社のLR6‐ILや既存の積層信号灯に追加して使用できるWDT-4LRがあります。)
STEP2:設備からの信号を集約してネットワークに接続する
SETP1で使用する出力機器に応じて信号を集約する機器を選定します。
たとえば無線中継器を使用した場合はセットで受信機が用意されているので基本的にはそれを使用します。
STEP3:アンドン(稼働状況)を表示する画面を作成する
集約した情報をアンドンとして表示するためのソフトはさまざまな企業が製品として販売しています。
ただし不要な機能も組み込まれており、価格が高く自由度が低いことがあります。
そこで活用したいのがエクセルを活用した表示ソフトです。
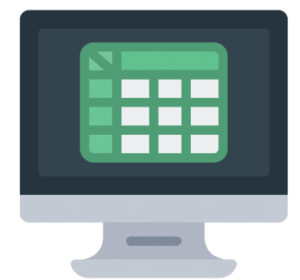
集約した信号を描画するプログラムは必要になりますが、必要最低限の機能だけに限定して始めることができ、初期費用が抑えられます。
また閲覧、操作、メンテナンスもエクセルから可能になります。
そのためプログラミングのような知識がなくても運用、メンテナンスができます。
上記は一例であり各現場に最適な方法を提案できますので、ご興味がある方は遠慮なくご連絡ください。
デジタルアンドンの応用
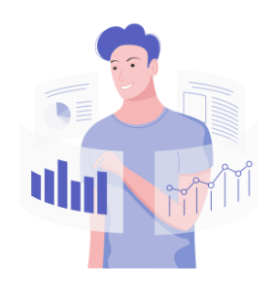
集約した信号はリアルタイムで稼働状況を把握する以外にデータとして蓄積することで稼働状況分析ツールとして活用できます。
いつ/どの設備が/どの程度(時間)/なぜ停止していたかがわかるようになります。
本来これを調査しようとすると専任の人を充てて調査する必要があります。
この分析ツールがあれば過去のデータを蓄積できるため、可動率低下の原因になっている設備の特定が容易になります。
さらに分析ツールは人材育成にも役立ちます。
本来、人がするべきは設備の特定ではなく、設備で発生している問題の真因追究と対策です。
対策実施のための時間を確保し、改善が進むことで働きがいが生まれ、人も成長することできます。
まとめ
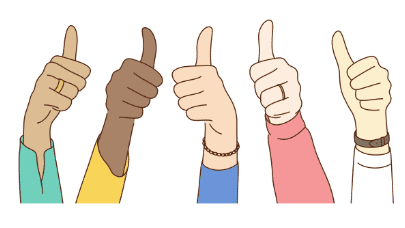
いかがでしたでしょうか。
「目で見る管理」は製造現場にとっては生産性、品質向上を目指す上でとても重要です。
それを実現するツールの1つがデジタルアンドンです。
IoT化が進む中でデジタルアンドンの導入に役立つさまざまな機器が登場しています。
各現場や目的によりコストや導入方法も変わります。
最初は必要最小限の範囲から始めて、手の内化ができてきたら範囲を拡大するのも良い方法です。
IoTはあくまでも手段で、これだけで生産現場が良くなることはありません。
正しく使い、分析して改善を実施することで初めて効果が得られます。
ムダな作業を低減し、人が考え行動できる環境を創り、改善が進む良いサイクルが回る現場を作りましょう!
しかし、「そうは言っても何から手をつけていいのか分からない」という企業様も多いと思います。
弊社では、中小企業の方々が業務を効率化するためのサポートをしております。
業務を進めるうえでの疑問や相談がありましたら、遠慮なくご連絡ください。
”日本のモノづくりを支えたい”
この弊社の信念のもと、小さなことからでもお手伝いをさせていただければ嬉しいです。
最後までお読みいただきありがとうございました。