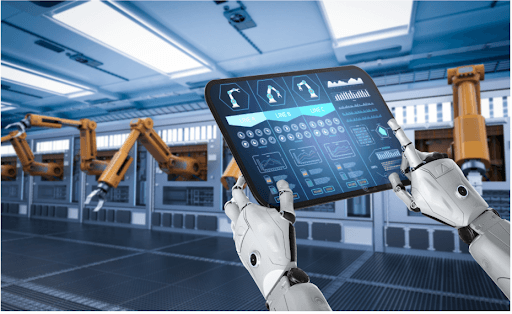
✅工場のデータ集計作業を効率化したい
✅データを活用して設総率を向上したい
❓工場DX化の進め方が分からない
❓誰に何を相談すれば良いか分からない
昨今話題にあがる工場のデジタルトランスフォーメーション(DX)化について
このような悩みを抱えている中小企業が多いのではないでしょうか?
工場のDX化を達成できれば、データ集計の効率化はもちろんのことデータ分析による早期アクションが可能となり、さまざまな場面で生産性向上が見込めます。
しかし、工場のDX化といってもなかなかイメージがわきませんよね。
こちらの記事では、筆者の業務経験にもとづき、工場DX化の目的や目指す姿、具体的な導入3STEPについて解説します。ぜひ参考にしてみてください。
目次
1. 工場DX化の目的と目指す姿
1-1. 工場DX化の目的
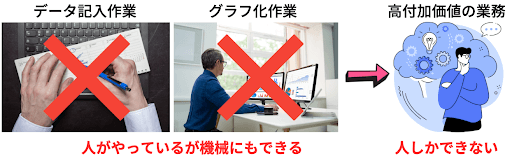
工場DX化の目的は、下記を目指した工場の生産性向上になります。
✅付加価値を生まない業務→機械やシステムに任せる
✅付加価値を生む業務→人が担う
例えば、工程におけるデータ記入やグラフ化作業は、付加価値を生みません。
グラフから工程の問題点を発見し、改善を通して工程の生産性を上げることが、付加価値を生む業務です。
単純作業は機械やシステムに任せ、改善の判断や遂行を人が担う工場を目指しましょう。
1-2. 工場DX化の目指す姿
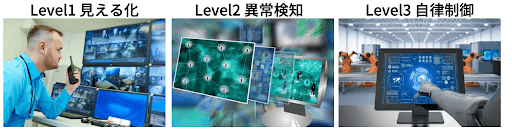
工場DX化により達成する工程の姿は、下記のLevel1〜3に分類することができます。
✅Level1 見える化:加工データや稼働状況を常時モニタ化
✅Level2 異常検知:異常の発生や兆候を自動警告
✅Level3 自律制御:異常になる前にパラメータを自動調整
本記事では“Level1見える化”の導入ステップについて解説します。
今後、Level2,3へ進むためにも、このLevel1に愚直に取り組んでおく必要があります。
モノづくりでいうとLevel1は製品設計にあたる重要なステップです。
ちなみに、Level2,3では、機械学習を用いた解析手法も登場します。
モノづくりの特徴によっては、極めて有効な手段になりますので、ぜひ導入検討ください。
2. 工場DX化(Level1)のメリット・デメリット
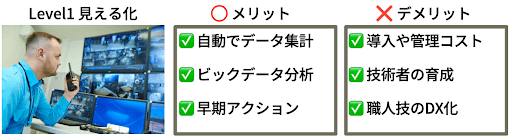
以降、本記事では、工場DX化の”Level1 見える化”について解説します。
導入にあたっては、メリット・デメリットを判断し進めていただきたいと思います。
2-1. 導入メリット
導入メリットは、主に下記の3点です。
✅自動でデータ集計:データ記入、集約、グラフ化の作業工数廃止
✅ビックデータ分析:膨大なデータから、結果に寄与する要因を瞬時に解析
✅早期アクション:問題発生→要因特定→対策のサイクルを早期に遂行
1つ目は、一番想像しやすいメリットだと思います。
実際、筆者の担当した工程では、約1時間/日の工数を低減することができました。
2つ目のビックデータ分析は、工場DX化によるメリットです。
自動データ集計により、過去数年分のデータを蓄積することができます。
例えば、不良解析においては、過去の不良発生のタイミングと工程データを遡って解析する事で、不具合要因を特定できます。
3つ目は、1つ目&2つ目の産物です。
稼働状況を見える化することで問題発生から対策まで早期に遂行できることにより、不具合や不良の被害を最小限にとどめることができます。
2-2. 導入デメリット
一方、導入のデメリットは、下記の3点です
✅導入や管理コスト:情報インフラの構築に伴う初期投資やシステムの維持管理コスト
✅技術者の育成:システムを維持管理するための人材育成コスト
✅職人技のDX化:職人技で成立する工程のDX化は投資規模が大きく困難
1つ目は、DX化検討において必ず通る壁です。
導入コストは精度よく見積もれる一方、非定常業務の効果見積もりが難しいです。
ただし、その前提でも、解決したい課題が大きい場合は経営判断で導入していくべきと考えます。
2つ目も重要な観点です。
自動集計システムを導入した後、様々なグラフ化や解析の要望が出ると思います。
都度、要望に対応しツールを使いこなせる人材の育成が必要です。
3つ目も注意が必要です。
包丁を作る工程を例にとります。
この工程で必要な情報は、全て職人の5感により取得されています。
この工程を全てDX化すると、膨大な機材費やデータ取得工数が発生し、経営が成立しません。
3. 工場DX化(Level1)の具体的な進め方3STEP
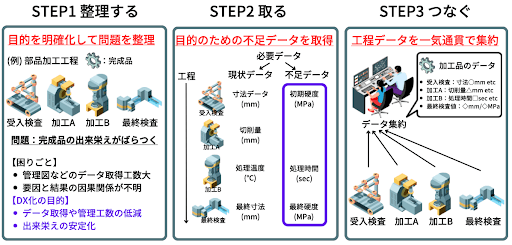
ここでは、より工程に落とし込んで、Level1(見える化)の進め方を解説します。
本記事で1番重要なパートなので、じっくり読んでいただけるとうれしいです。
まず初めに、3STEPの結論をいいます。
✅STEP1 “整理する” :目的を明確化して問題を整理
✅STEP2 ”取る”:目的のための不足データを取得
✅STEP3 “つなぐ”:工程データを一気通貫で集約
Level1における効果出しや、第1章で述べた工場DX化のLevel2,3につなげるためには、このSTEP1の整理が最も重要です。
業務品質の8割以上を決めるといっても過言ではありません。
筆者も、ここをおろそかにして、後から足元を救われたことが何度もあります。
3-1. STEP1 ”整理する”
まず初めに、解決したい工程の問題点を明確にしましょう。
本記事では、データを取得していることを前提に話を進めてますが、何故データを取っているのでしょうか。
設備不具合や不良品が全く出ない工程だったら、データ取得や管理の必要はありません。
裏を返せば、管理すべき結果や要因系があるということです。
そのため、今一度、下記を整理する所からはじめます。
✅管理したい結果系データは全て取れているか
✅結果系にひもづく要因系データは取れているか
✅取るべきデータの頻度や精度は必要十分か
上記が一つでも抜けてしまうと、結果何も使えないデータとなってしまいます。
現状、抜け漏れなくデータが取得できているならば、STEP3へ進みます。
3-2. STEP2 ”取る”
STEP1で取得データに抜け漏れがある場合は、愚直にデータを取得しましょう。
データ取得で気を付けるポイントは、下記の2点です。
✅インラインで全数検査するか/アウトラインで抜き取り検査するか
✅製品1ケ1ケに対してデータのトレーサビリティが取れているか
1つ目の視点は極めて重要です。
データが材料ロットで変動する場合は、材料ロット毎の抜き取り検査で取得します。
一方、全数検査が必要だがインライン計測機が存在しないこともあります。
この場合は、全数検査が可能な代替物性の取得を検討します。
2つ目の視点も重要です。
要因系が結果系と1対1で紐づいてなければ、解析しても因果関係を導けません。
製品にQRコードを印字し読み取る手法や、物体固有の”指紋”をAIで検出し、印字レスで識別する手法などもあります。
ぜひ、様々な手法を検討してください。
3-3. STEP3 ”つなぐ”
最後は、工程間のデータを集約し、一元化します。
✅ネットワークやサーバー等のインフラ整備
✅集約したデータを市販ソフトを活用してグラフ化・解析
データの転送や集約は、自社のネットワークやデータ取得頻度に適した最適な方法で構築してください。
また、集約したデータを、どのようなソフトで処理し活用するかも検討していきます。
モノ作り業界においてビックデータ収集や解析が進んでいる半導体業界では、YDC SONAR*が有名です。*https://www.ydc.co.jp/service/sonar/ydcsonar.html
4. 工場DX化の実例
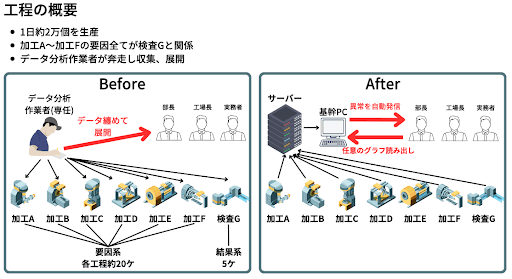
次に、工場DX化における筆者の業務経験を、簡単に紹介したいと思います。
対象は、上記にあるような1日約2万個の部品を生産するラインで、加工AからFの工程が検査Gの結果に関係します。
1日に生成されるデータ数は、要因と結果系を合わせて約250万個になります。
工程で異常が発生すると、専任のデータ分析作業者が250万個の中から必要なデータを抜き出します。
そして、手動でデータをまとめグラフ化し、関係者にメールで展開します。
かなり手間と労力がかかっているのが分かりますね。
そこで、この工程にDX化を取り入れました。
データをサーバーに集約し、基幹PCで処理をします。
これにより、工程で異常が見つかった場合は、関係者に自動で発信することができるようになりました。
もちろん、専任のデータ分析作業者は不要です。
また、関係者は必要なタイミングで工程のデータを見れるようになり、業務効率化に繋がりました。
これらは、第1章で述べた所のLevel1(見える化)とLevel2(異常検知)ができていることになります。
筆者は、Level3(自律制御)の工場をそんなに見たことがありませんが、少なくともこのLevel1,2まで進めることができれば、工場の姿はかなり変わります。
5. 工場DX化の今後の展開とまとめ
いかがでしたでしょうか。
工場DX化を通じて、生産性を格段にあげることができます。
一方で、進め方を間違えると後戻りが大変なので、愚直に進めていただきたいと思います。
しかし「そうは言っても何から手をつけていいのか分からない!」という企業様も多いと思います。
弊社では、そんな企業様に向けて初期のご相談からお受けしております。
業務を進めるうえでの疑問や相談がありましたら、遠慮なくご連絡ください。
“日本のモノづくりを支えたい”弊社信念のもと、小さなことからでもお手伝いをさせていただければ嬉しいです。
最後までお読みいただき、ありがとうございました。